研报简读《半固态电池专题报告:向理想更近一步》
一
半固态电池寸积跬步,向理想更进一步
(一)固态电池兼顾安全和性能,是理想电池形态
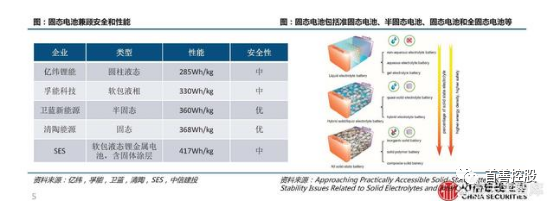
“固态电池”涵盖了一系列宽泛的概念(以电池内部的液相占比大致区分):准固态电池、半固态电池、固态电池和全固态电池等。 固态电池研究者一般认为,固态电池的能量密度更高、安全性更强。我们从部分公开了电池单体能量密度的企业信息出发直接比较, 固态电池确实可以在一定程度上具备较高质量能量密度。
(二)向固态化过程核心在电解质,多方面性能问题仍待解决,半固态电池寸积跬步
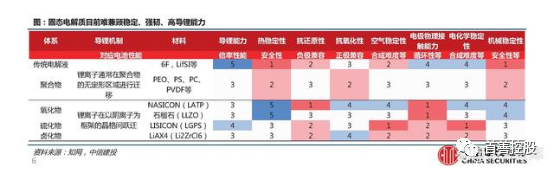
固体电解质和电解液一样,都应考虑离子导通、电子绝缘、和电极的物理接触良好、抗正极氧化、抗负极还原(对高能量密度电池来 说对锂金属的稳定性非常重要)、电化学稳定、热稳定、空气稳定、机械稳定、各个指标的对应温度特性好等性能需求,以及综合成 本低廉的规模推广需求。各类固体电解质的性能表现各有所长,但是任何单一固体电解质均无法取得令人满意的综合性能。整体看硫化物电导率可媲美液态电 解液但稳定性较差,氧化物热稳定性较好但抗还原能力、物理性较弱,聚合物抗还原性较好且物理接触较好但电导率较弱。固体电解 质材料开发,固体电解质和电解液协同应用至关重要,是非常系统的工作,单一或复合电解质可优化的空间较大,半固态电池寸积跬步。
(三)半固态当下典型的工艺是原位聚合,可以兼顾固液优点
凝聚态电解质即加入少量电解液使电极材料和电解质间保持良好的界面接触,再利用化学或电化学反应进行原位聚合 ,使液体电解质部分或全部转化为固体电解质的方式,解决部分界面问题(主要是循环性能),在电池体系设计上更 易实现性能、成本兼顾。
(四)理论上,半固态或兼备固态电解质和电解液优点
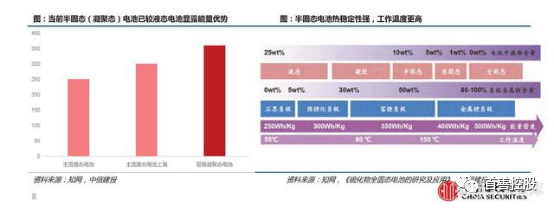
就电芯能量密度而言,目前主流三元液态电池达到200-300wh/kg,已接近能量密度上限,而卫蓝新能源、国轩高科的半固态(凝聚 态)电池已达到360wh/kg,初步显露优势。安全性方面,半固态(凝聚态)电池电解液质量分数仅为5%-10%,固态电解质的不易燃、零挥发,显著提升了电池的热稳定性。
二
优化方向:复合电解质、新型锂盐、高性能正负极、隔膜涂覆、多方面优化
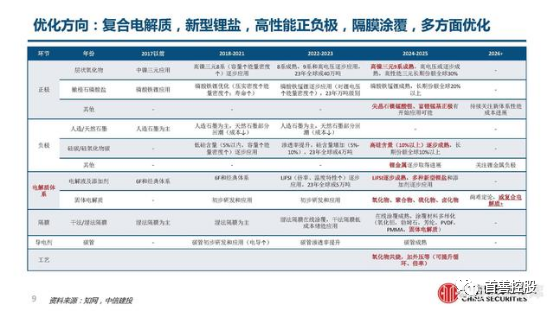
(一)能量密度优化方向:高性能正负极,多方面优化
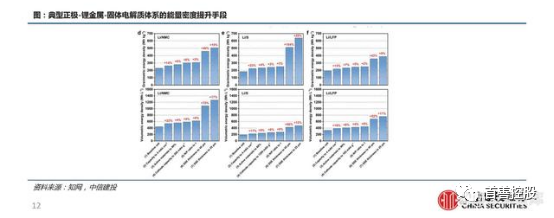
量产/接近量产的100Ah以上固态电池,质量能量密度可实现性在300Wh/kg以上。在实验室水平,固态电池的能量密度可以更高。硫(载于碳管上)正极-LGPS-锂铝合金负极电池(标准2032纽扣电池,估算在0.3Ah级别)的质量能量密度达到541Wh/kg。三元正极(包覆氧化锂-氧化锆纳米层)-LPSCl固体电解质-银碳复合负极电池(0.6Ah软包电池)的体积能量密度可达900Wh/L。
电池的能量密度提升手段:提升电极面密度;提升正极中活性物质的含量;提升正极容量密度;提升N/P;减薄电解质厚度。充分减薄固体电解质,则三元正极-锂金属电池的体积能量密度表现突出,硫正极-锂金属电池的质量能量密度表现突出,铁锂正极的性 能指标变化幅度略小,能量密度也较低。
(二)倍率性能优化方向:硫化物、卤化物掺杂+电解质减薄
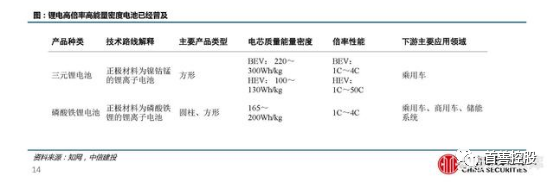
1. 倍率性能优化:对电池性能至关重要
锂电池的快充性能需要考虑电解质的(体相、电解质-电极界面)离子电导率,也需要考虑其他组元(比如锂金属负极)在较高倍率条 件下可能存在的问题。典型能量型液态锂电的倍率性能在1-4C范围,功率型液态锂电的倍率性能高达几十C。也有部分企业宣传其超级 快充液态锂离子电池的倍率性能可以进一步提升。固体电解质的离子电导率一般来说低于电解液,电解质-电极的界面阻抗也较高,这使得固态电池在倍率性能上不易和液态电池竞争。优化方向相对综合,依托硫化物、卤化物电解质掺杂,结合减薄工艺等进行提升。
离子电导率是决定电池倍率性能的重要指标,固体电解质的离子电导率一般来说低于电解液,电解质-电极的界面阻抗也较高,这使得 固态电池在倍率性能上不易和液态电池竞争。面对快充困境,卤化物潜力有待挖掘。研究者合成了Li2In1/3Sc1/3Cl4固体电解质,该电解质搭配钴酸锂或者高镍正极、锂铟合金负 极后,在相对高的倍率(2-3C)条件下,还保留了较高的容量,这也体现了卤化物体系的潜力。
2. 倍率性能优化:减薄固态电解质是较有效的方法
固态电解质厚度会显著影响电池性能:固体电解质厚膜不仅会降低固态电池的能量密度,而且还会显著增加膜厚度方向的离子传输距 离,从而产生较大的电压极化和电池内阻,从而降低倍率性能。对固态电解质减薄将成为提升固体电解质材料的锂离子电导、降低电子电导的有效手段。Quantumscape宣称其单层固态电池在加外 压的条件下可以实现4C(实际约3C)快充,而且属于无负极锂金属电池。
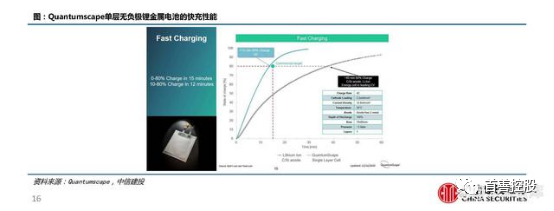
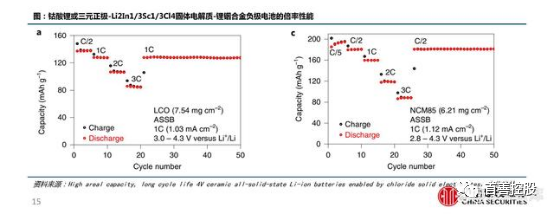
3. 倍率性能优化:最新倍率性能实现室温1℃,高温20℃
当前最新研究显著提升固态电解质的倍率性能,实验室条件下实现了室温1C,且保持了电池容量:研究者设计了复合电解质,对应的高镍三元正极(复合了约30%固体电解质,所以容量有摊薄)-复合硫化物电解质-石墨薄层-锂金属 负极电池样品实现了室温1C,55度下最高20C(电池大幅加外压;到5C时容量衰减都不大)的倍率性能。且研究者合成的固体电解质 Li9.54Si1.74(P0.9Sb0.1)1.44S11.7Cl0.3 (称LSPS)作为主体电解质对应正极的实际容量最高,超过前述LGPS等固体电解质。固态 电池倍率性能优化未来可期。
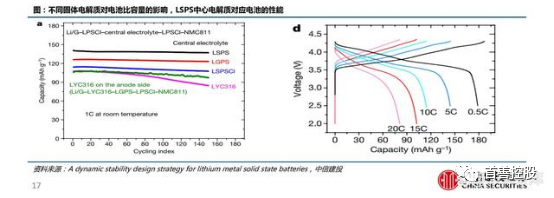
(三)循环寿命优化方向:聚合物骨架+外压
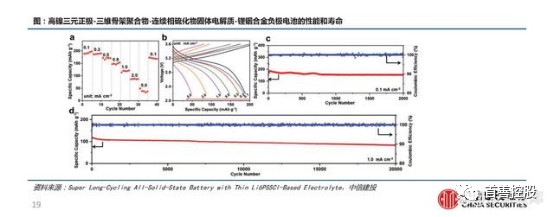
有研究者用静电纺丝-渗透-热压工艺制备了聚偏氟乙烯-三氟乙烯-LPSCl固体电解质膜,搭配LPSCl-铌酸锂包覆的高镍三元正极、锂铟 合金负极制成电池并施加外压。部分低正极载量样品在1.61C倍率下体现了超过20000次的循环寿命(容量保持率70%以上)。
(四)安全性优化方向:正极载量和电解质厚度是关键
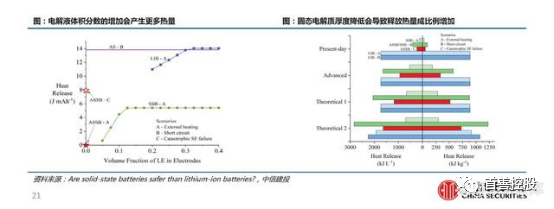
固体电解质的安全性有较大程度提升,但仍存在安全隐患:固体电解质的致密度并非百分之百,这使得外部环境加热温度较高时正极 释放的氧可以扩散至负极;一定条件下固体电解质中也会生长锂枝晶,可能触发内短路。固态电解质厚度成为关键因素:在使用热稳定性较高的LLZO电解质时,固体电解质较厚、正极载量较低的情景下固态电池在经历外部 加热、短路、机械破坏等滥用时表现较好;但减薄电解质、加厚电极的场景固态电池表现一般。
(五)体系的优化方向:复合体系是基础
1.体系上,有机物与无机物混合体系是必然方向
倍率性能和循环性能的短板核心还是半固态电解质导锂能力弱, 目前聚焦这两个问题解决方法的基础是复合固态电解质,结合工艺和正负极调整实现性能优化,如PEO掺LLZTO优化电导率,LATP隔 膜涂层+包覆LITFSI的PEO,可以兼备机械性能、电导率、热稳定性和电压等优势。
如有研究工作表明,在PEO中掺杂石榴石结构的LLZTO锂镧锆钛氧固体电解质(12.7%体积分数),掺杂后导锂活化能显著降低;不同的LLZTO粒径效果不同,40nm颗粒的效果最好。
有研究者以LATP为涂覆层,和聚乙烯隔膜复合,并在复合隔膜的孔隙中及外侧填充/包覆掺杂LiTFSI的PEO,获得复合固体电解质。该固体电解质和磷酸铁锂正极-锂金属负极组成固态电池后,60℃时以0.2C倍率循环200次,容量几乎没有衰减;而且在折叠、剪切等 操作后,电池都非常安全。也有研究者以1%质量分数的LLZTO包覆正极,LLZTO高温时作为补锂剂,延迟正极层状结构的不可逆分解,抑制正极释氧并提升安全性。
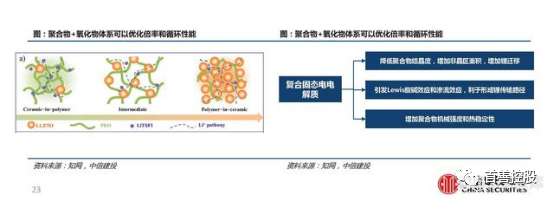

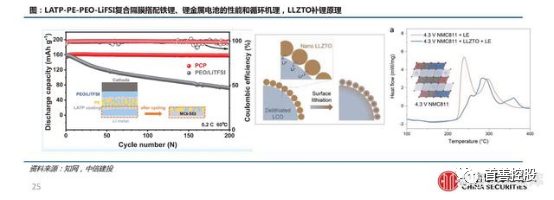
2.与此同时,锂盐的选择至关重要
预计未来一段时间仍是固体电解质和电解液协同应用,部分体系即使全固态也需要加入锂盐,锂盐及添加剂的选择至关重要,目前看 较典型的三类锂盐各有优劣,传统液态电解液中电解质以LiPF6为主,半固态中添加电解液预计以高浓度LiTFSI和LiFSI为主,核心考 虑是满足热稳定性和化学稳定性等要求。
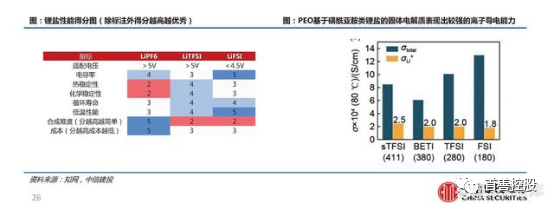
三
工艺:前段工序相同,后段增加加压或烧结
(一)前段工序相同,后段增加加压或烧结
对比分析典型锂离子电池、钠离子电池、锂硫电池,固态电池和锂空气 电池的生产工艺流程(概念有交叉但不失一般性)。从前段工序来看,固态电池的工艺和液态电池总体区别不大,但锂金属 负极的应用、固体电解质混料与包覆处理需要额外的工艺流程。从中、 后段环节来看,固态电池需要加压或烧结,不需要注液化成(固液混合 电池则和常规液态电池类似仍然要注液化成)。
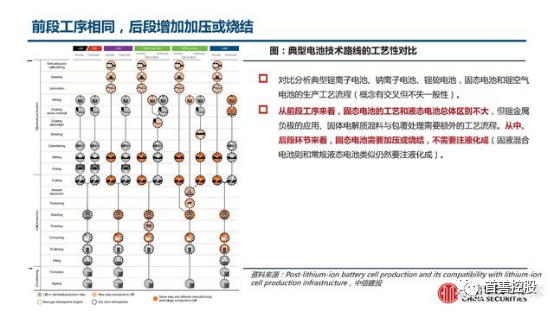
(二)工艺上看,氧化物烧结,硫化物加压,聚合物绕卷预计是必备的工艺
有研究者归纳:氧化物需要烧结;硫化物需要加高压且对气氛很敏感;聚合物卷对卷工艺原理简单但也面临容易短路等问题。有研究 者将固态电解质的生产工艺分为湿法、干法两条路径,不同路径各具优势。我们认为,干法制取粉体比湿法生产料浆更便捷,湿法涂布后卷绕/叠片比干法烧结更利于规模化;选择聚合物-无机物复合,或者原位 固态化的固体电解质路线,最终成功规模化的概率更高。
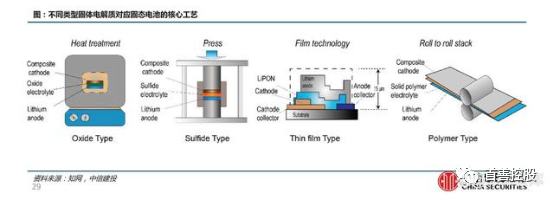
(三)湿法制膜:效率高、接触好
湿法制膜工艺:利用极性溶剂、粘结剂和正极活性物质或电解质配成均匀溶液,再将溶剂蒸干得到电解质膜。具有以下优势: 效率高:极性溶剂的使用可以缩短正极活性材料或者电解质的分散时间 。改善固固接触:活性材料或电解质溶液可以填充膜的空隙,缓解颗粒之间较差的固固接触,有利于进一步提高电极载量,提升电解质的强度。
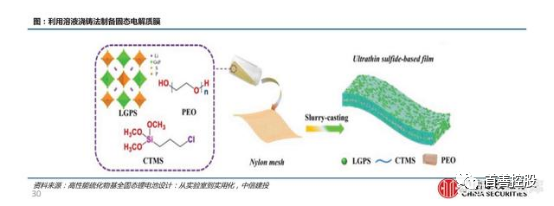
(四)干法制模:成本低、产品薄
干法制膜主要是利用粘接剂和活性材料或电解质混合,通过辊压等机械方式压制成膜。其主要有以下优点:成本更低:不需要任何溶剂或蒸发设备,因此可以进一步降低成本;有利于更厚的电极、更薄的电解质膜的生产:可以通过控制压力实现无裂纹、更厚、载量更高的电极膜及更薄的电解质膜,从而进一步提高电池的能量密度;保持硫化物电解质的结构完整:不再需要采用有机溶剂,避免对硫化物电解质结构的破坏;粘接剂使用减少:干法制膜工艺可以显著减少粘接剂的数量,从而减轻粘接剂对离子传到的阻碍作用。
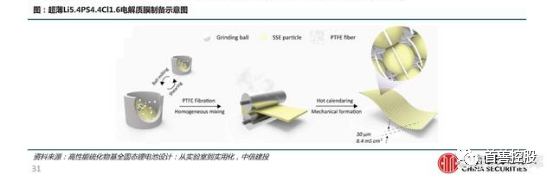
四
成本及空间:成本仍需努力,预计2030年300GWH需求
(一)成本仍需努力,电池设计仍不成熟,差异较大
固体电解质的单位成本随材料体系不同有所不同,用量不同也有带来了 巨大的成本区别;电极用量、处理工艺和电池制造、成组也有不确定性。根据报道硫化物固体电解质对应的固态电池成本更低。国内部分厂商披露半固态电芯成本在3元/Wh左右。和现有的液态电池体系作对比,固态电池如试图取得单位能量的成本优势,需要同时在固体电解质降本减量、电极适配、电池制造等方面取得显著进展。
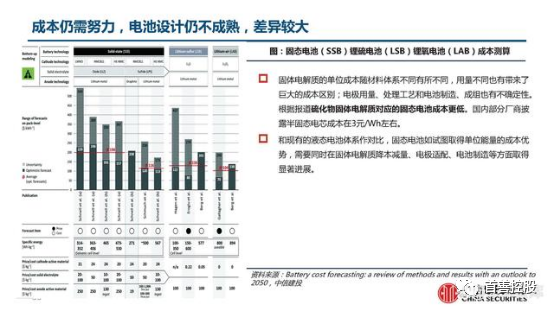
(二)需求空间:预计2030年需求300GWh,渗透率6%,增速较快
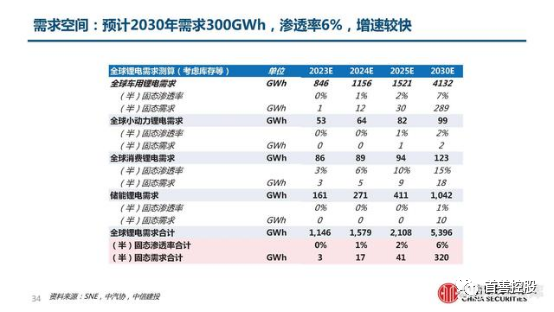
五
产业链进展
核心问题解决将带来相关领域放量,关注电解质从0-1、高性能材料放量向全固态体系探索过程中,诸多环节技术路径存在不确定性,半固态电池相关体系已有雏形,核心问题解决将带来相关领域放量。
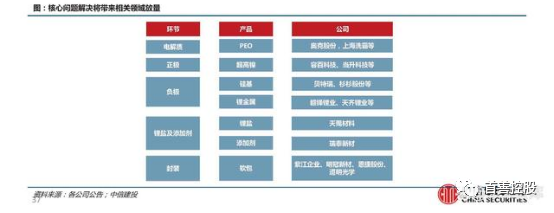
【原文发表在首善控股公众号】
【 end 】